We’ve been looking at ways to disbond structural adhesives for about 10 years, and working with the National Composites Centre through the Technology Pull-Through Programme has enabled us to prove the technology readiness of our research. We can now work with industry to fully optimise the technology for specific applications and tailor it for them as required.
Facilitating the industrialisation of proven technologies
The High Value Manufacturing Catapult is comprised of seven world-class centres of industrial innovation co-founded with our University partners: Sheffield, Bristol, Strathclyde, and Warwick. With active links in over 50 UK academic institutes, the High Value Manufacturing Catapult collaborates with a broad range of academic and industry partners to translate research into economic impact.
All seven High Value Manufacturing Catapult Centres are part of the ISCF [1] ‘Driving the Electric Revolution’ (DER) consortium working alongside 23 universities and two other Catapults, in a national programme to seize the economic opportunities from the global transition to clean technologies and electrification.
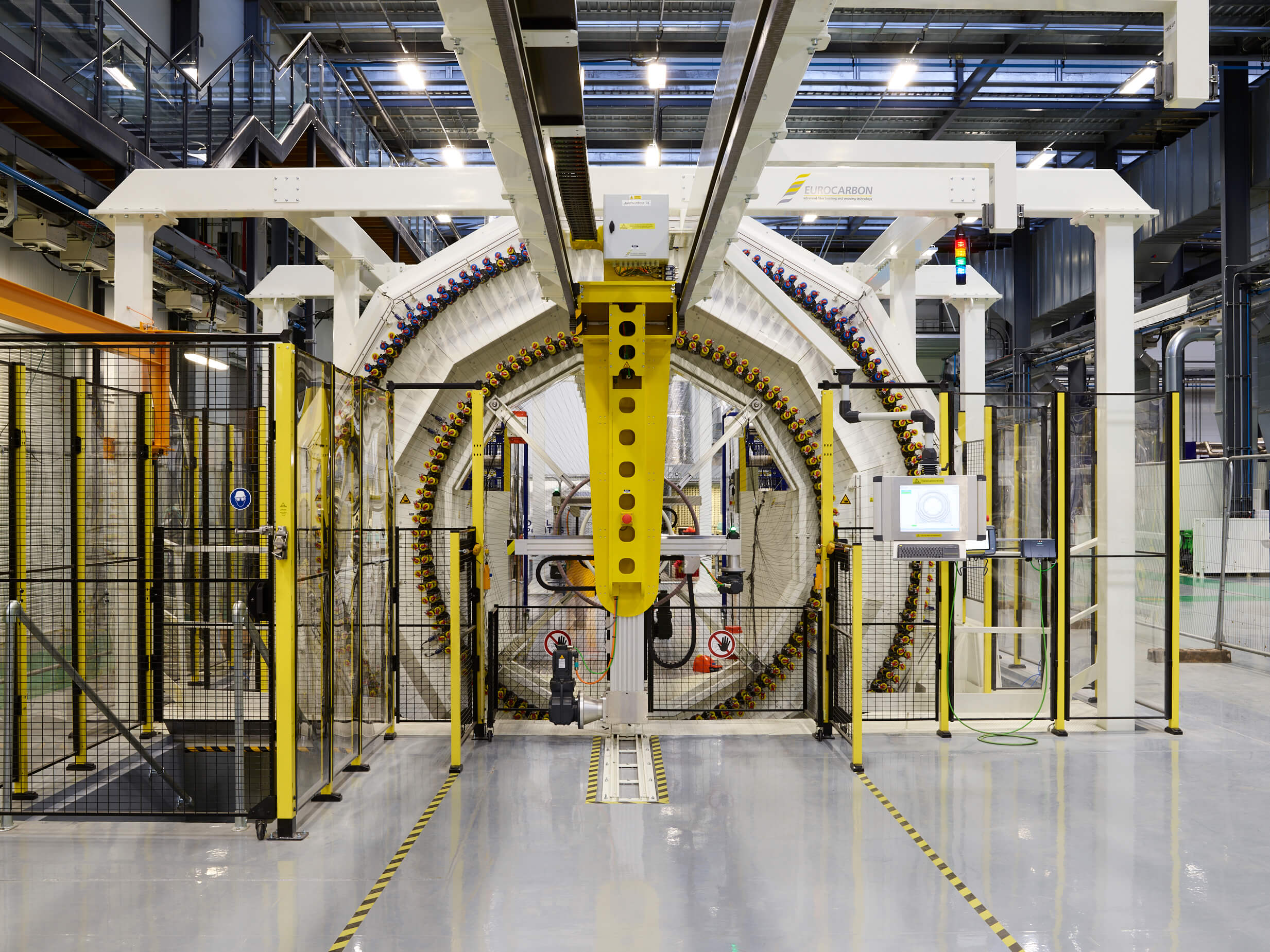
The National Composites Centre’s (NCC) Technology Pull-Through Programme (TPT), launched in 2017, promotes research that will enable the transition of suitably mature technologies from academia to industry. It aims to de-risk, scale up and facilitate the industrialisation of proven technologies by transferring them from the lab environment into the NCC’s semi-industrial set-up for further testing. With over 30 projects funded to date across the UK the TPT is managed by NCC and collaboratively run between NCC and the academic partners.
The Dismantlable Joints project is part of the TPT in collaboration with Oxford Brookes University. The project aimed to validate and increase the Technology Readiness Level (TRL) of the University’s academic work on adhesive disbonding technologies.
Replacing mechanical fixtures with bonded joints can reduce assembly time and decrease structure weight, however modifications and disassembly of these components are complex due to the irreversible nature and high strength of the structural adhesives used.
Researchers at Oxford Brookes University demonstrated that by adding low-cost additives to off-the-shelf structural adhesives, composite parts could be separated in as little as six seconds by raising the temperature of the joint to approximately 160°C. The NCC proved that the new approach works at an industrial scale as part of the Technology Pull-Through Programme.
This means, in the near future, composite components may be easily repositioned and reused during manufacturing – reducing waste, repaired in operation and recycled more efficiently at the end of their working life.
By making it easy to work with, repair and disassemble composite parts, this world-leading research could have a transformational impact on the design, use and end-of life recycling of wide range of products, including cars, aircraft and wind turbines.
[1] Industrial Strategy Challenge Fund